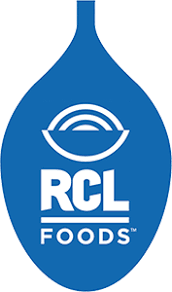
Share this post on
To apply, click on the link at the end of the posts and all the best with your applications.
HOD – Maintenance
Closing Date
2024/08/14
Reference Number
RCL240731-2
Company RCL Foods
Job Title HOD – Maintenance
Functions Engineering
Job Type Classification Permanent
Location – Town / City Pietermaritzburg
Location – Province KwaZulu-Natal
Location – Country South Africa
Job Description
RCL Foods is recruiting for a driven, highly energized and Operational focused HOD – Maintenance within the baking business unit.
The suitable candidate will be responsible to manage all operational maintenance requirements related to the production of baked goods both effectively and efficiently. To administer and manage within budget the plant equipment (efficiency and availability) so that all baked goods are delivered on time and in full, at the right quality.
This role will be based in Pietermaritzburg and reporting to the Operations Executive.
This role is a Permanent role.
Minimum Requirements
Qualifications
Grade 12
NQF level 5/6, Diploma or Degree in Operations Management
Qualified, trade tested Artisan
Experience
10+ years manufacturing management experience, preferably with FMCG and perishable food background
Competencies
Operational Decision Making
Planning & Organising
Information Monitoring
Inspiring Leadership
Building a Successful Team
Managing Conflict
Quality and Results Driven
Skills/Knowledge
Practical knowledge of ERP system, JDE advantageous
Full understanding of OHS systems
Good computer literacy, especially Excel
Duties & Responsibilities
Maintenance
- Make recommendations on new machinery and equipment for capital expenditure.
- Establish minimum critical spare stock levels to ensure it is maintained and well managed within departments. Spare parts for different machineries to be utilized within budget.
- Manage Sunshine engineering team and maintenance projects and ensure on time delivery of projects.
- Ensure preventative and scheduled maintenance schedules are in place and actioned.
- Monthly review of job cards.
- Ensure plant uptime targets are set and met.
- Measure and report on machine utilisation and costs.
- Establish a capex replacement/plant upgrade policy metrics.
- Prepare annual budget prior to start of new financial year.
- Ensure daily floor walks are conducted and preventative maintenance is identified and incorporated into the planned maintenance schedule.
- Work with HOD Production to identify improvements to be made on machinery to improve production efficiencies
Utilities Monitoring
- Monitor the consumption patterns, activities and or costs
- Continuously come up with initiatives to address all the inefficiencies within the utility spectrum.
Labour
- Ensure appropriate staff level and training programmes to meet business requirements.
- Ensure that labour cost is effectively and efficiently managed, aligned to budget.
- Review planned labour hours against actual labour hours.
- Review outsourced labour hours monthly.
- Make recommendations to achieve savings in labour costs.
- Ensure that staff are certified and approved on TracTech monthly.
- Ensure monthly payroll is approved.
Quality, Health and Food Safety
- Ensure and maintain audit compliance with Occupational Health and Safety and Safety Audit.
- Ensure that the plant is audit ready every day.
- Ensure all machinery equipment IOD ‘s are investigated within 48 hours of the incident and corrective actions taken and implemented within timelines appropriate to the severity.
- Work with H&S managers to ensure OSH requirements are implemented timeously.
Legal Compliance
- Ensure that all legislative and industry standards are achieved, and timeous action is taken where required to ensure that there are no areas of non-compliance within maintenance.
- Ensure all electrical equipment and installations are maintained or installed in accordance with statutory requirements and business needs.
- Implement maintenance occupational health and safety compliance with all relevant legal requirements.
- Ensure all building and equipment utilization is in accordance with risk, security, safety, health, HACCP and ISO22000, 45000 and 18000 standards.
- Monitor and verify contractor compliance with the OSHACT and authorize access for complying contractors to site.
- Ensure that all the statutories are maintained as per the relevant OHSA regulation. Pressure vessels, lifting equipment, machine guarding and that a safe working environment is maintained at all the time.
- Find opportunities to implement better working practices regarding ISO, environmental, health and safety.
Leadership
- Conduct weekly meetings with teams.
- Promote harmonious relationships with staff.
- Identify training and development needs.
- Provide on the job training.
- Conduct succession planning programme.
- Ensure the maintenance staff reflects the company image.
- Ensure team is motivated.
- Performance manage subordinates.
- Ensure effective and efficient communication with line managers.
- Ensure effective commination with team members.
- Ensure effective communication with suppliers.
- Effectively cooperate with all departments in particular HOD Production.
- Correspond with other departments to correct errors.
- Drive the culture and vision of the Company.
- Reward and recognise star performers.
Reporting/Budgets - Ensure effective and accurate reporting on JDE/ERP
- Review and report on monthly expenses relative to budget.
- Review and contribute to monthly GM reports.
- Compile monthly reports.
- Complete budgets and forecasts for GM approval. Track same monthly expenditure.
- Work with HOD Commercial to identify improvements so that maintenance reporting can be derived from JDE
Special Projects
- Partake in departmental ad hoc special assignments or tasks.
- Obtain relevant desired results for any ad hoc projects having prioritised it with other regular activities.
- Initiate personal growth and development.
- Ensure that you actively participate to successfully comply with the plan of action identified in your performance appraisal and any training initiatives you attend.
- Compliance with all company policies and procedures
- Act in the best interests of the company and the department.
- Be available to assist with additional tasks or work overflow.
Artisan: Fitter Turbines Designate
Closing Date
2024/08/04
Reference Number
RCL240725-2
Company RCL Foods
Job Title Artisan: Fitter Turbines Designate
Functions Engineering
Job Type Classification Permanent
Location – Town / City Pongola
Location – Province KwaZulu-Natal
Location – Country South Africa
Job Description
RCL FOODS is searching for an experienced Artisan: Turbine Fitter designated to join our Sugar Division based in Pongola. The position requires an individual to Conduct regular inspections of the turbines and associated equipment/machinery to ensure that the work performed meets the required standards to minimize downtime.
Minimum Requirements
Trade test Certificate (Mechanical Fitting or Fitting and Turning) and proof of the successful completion of a formal Institutionalised Training Programme is essential.
Minimum of three (3) years working experience as a trade tested Artisan Fitter/Fitter & Turner
Previous working experience as an Artisan Fitter Turbines will be an added advantage.
Experience in maintaining and fault-finding hydraulic systems is crucial.
Working knowledge of planned maintenance systems.
Well-developed interpersonal and communication skills.
Be prepared to work planned and unplanned overtime.
SAP system knowledge would be an added advantage.
Be prepared to do stand-by duty.
To be considered for appointment, the candidate must be a South African citizen.
Duties & Responsibilities
The primary objective of this position is for the incumbent to undergo a training and development as a Turbine Fitter.
Conduct regular inspections of the turbines and associated equipment/machinery to ensure that the work performed meets the required standards to minimize downtime.
Clean oil filters and strainers on turbines, gearboxes and shredder lubrication systems as required.
Maintenance of the turbines and other plant equipment in accordance with good engineering Standards and always adhere to ISO Standards and/or Procedures.
Attend to all breakdowns and/or stoppages in the respective section immediately.
Investigate any recurring faults and rectify the same.
Report any accidents, or incidents immediately to the Foreman: Extraction Maintenance.
Promote and maintain a safe and healthy working environment.
Maintain and uphold RCL Foods Quality Standards (High Standard of Workmanship).
Maintenance Clerk
Closing Date | 2024/08/01 |
Reference Number | RCL240725-1 |
Company | RCL Foods |
Job Title | Maintenance Clerk |
Functions | Engineering |
Job Type Classification | Permanent |
Location – Town / City | Spartan |
Location – Province | Gauteng |
Location – Country | South Africa |
Job Description
RCL FOODS is seeking a Maintenace Clerk to join our Baking Division based at Spartan. The position supports the Department in all administrative, clerical, scheduling and engineering procedures and other tasks as assigned by the engineering management within the scope of the maintenance department.
Minimum Requirements
QUALIFICATION AND EXPERIENCE
Grade 12 or N3 or NCV Technical qualifications.
Minimum of 2 years’ Maintenance experience preferably within the FMCG environment.
Health and Safety Experience.
Basic Computer certificate.
KNOWLEDGE AND SKILLS REQUIREMENTS
A working knowledge Computerized Maintenance Management Systems (CMMS).
Knowledge of Excel, Word, and PowerPoint.
An understanding of engineering machines components such as shafts, bearings, v-belts, drives, contactors, conveyors etc.
Knowledge of food safety standards is advantageous.
Knowledge of Document control.
Knowledge of safety and permit issuing.
Ability to think logical and problem solving.
Ability to interpret data and analyze.
Ability to analyze the trends in performance parameters.
Attention to details.
Duties & Responsibilities
Ensure all maintenance activities and data is captured on Pragma maintenance system.
Create work orders whenever required to do so by maintenance personnel’s.
Ensure data is captured related to electricity, water, and diesel usage.
Develop reports on maintenance efficiency and energy utilization.
Generate reports on outstanding work, maintenance efficiency, and status of compliance to SHERQ documentation system and audits.
Ensure that all SOP’s related to the Engineering function is up to date.
Maintain and update Pragma maintenance system to aligned work performed by Artisans Technical assistant and contractors.
Assist Maintenance Planner, Senior Artisans, Engineering Manager and Production Managers in planning downtime on equipment for PM.
Update Engineering SOP’s to ensure compliance with ISO 14001, 45001 and RCL Foods Quality System.
Ensure maintenance documentation filing system is maintained and up to date.
Ensure relevant equipment information on Pragma System to develop a comprehensive database of all Engineering related activities and usages.
Adheres to standard operating procedures.
Provide training to Engineering Staff on Quality, Safety and Pragma Management System.
Provide training to new pragma users on how to create work orders on ONKEY pragma system and update training to the present users.
Present engineering toolbox talks to engineering Artisans and Technical assistant.
Ensure maintenance staff timesheet data is correctly captured on best time.
Update maintenance schedule on Pragma maintenance system in conjunction with Senior Artisan’s and Maintenance Planner.
Assist with capturing of job cards for all engineering works Set up engineering safety meetings and update minutes Constant liaison with SHEQ department on ongoing developments Manage NCAs and CARs and lead in driving their closing based on root cause analysis Constant driving of audit compliance issues including attending to audit meetings.
Maintenance Administrator
Closing Date
2024/08/03
Reference Number
RCL240724-1
Company RCL Foods
Job Title Maintenance Administrator
Functions Engineering
Job Type Classification Permanent
Location – Town / City Pretoria West
Location – Province Gauteng
Location – Country South Africa
Job Description
RCL FOODS is seeking a Maintenance Administrator to join our Baking Division. The position supports the Department’s Administrative and systems function. The role will be based in Pretoria West and will report to the Maintenance Manager.
Minimum Requirements
QUALIFICATION AND EXPERIENCE
Grade 12.
Minimum of 2 years’ Maintenance experience preferably within the FMCG environment.
Health & Safety Experience
KNOWLEDGE AND SKILLS REQUIREMENTS
Sound knowledge of the plant and processes
Sound knowledge of Health & Safety systems.
Computer literate in both Microsoft Excel and Microsoft Word
Knowledge of ERP/EAMS (On-key, Bestime, Syspro, etc.)
An understanding on performance of relevant maintenance activities
Sound understanding of equipment reliability and performance.
Ability to plan and schedule maintenance related activities.
Compile, create and interpret report graphs.
Duties & Responsibilities
KEY RESPONSIBILITIES
Assist Maintenance Planner with planning activities according to professional planning standards.
Ensure that best practices in planning are applied to improve the efficiency of maintenance.
Implement and maintain a proper maintenance strategy and philosophy.
Initiate and manage preventative maintenance of all sections.
Updating & managing of Bestime time keeping of department.
Conduct Health & Safety inspections & Monthly requirements within department.
Assisting Maintenance Planner with Health & Safety Statutory Pragma Onkey System.
Ensure that all necessary documentation to perform the maintenance work are available.
Schedule Building maintenance work.
Ensure that Key Performance Indicators are captured and reported.
Production Manager
Closing Date
2024/08/02
Reference Number
RCL240723-3
Company RCL Foods
Job Title Production Manager
Functions Operations/Manufacturing
Job Type Classification Permanent
Location – Town / City Pretoria West
Location – Province Gauteng
Location – Country South Africa
Job Description
As a leading player in the Food Manufacturing industry, we pride ourselves on delivering high-quality products and making a positive impact. As we continue to grow, we are seeking a talented and motivated individual to join our team as a Production Manager.
The job holder will be required to manage the manufacturing of value-added Mixes (Coatings, concentrates on old and new premix lines) and packing of wheat and maize products, at the Pretoria Milling site in the most cost-effective way ensuring maximum efficiency and optimal mix whilst maintaining compliance with legislation, customer specifications, food safety, and quality standards to achieve production plan targets and determine and drive best practices, benchmarking and consistency management across the Department.
The role reports to the Operations Executive and is based in Pretoria West.
Minimum Requirements
Qualifications:
A Diploma/ Degree in Production Management or Degree/ Diploma in industrial/ Mechanical/ Electrical Engineering
A Wheat or Maize Milling qualification and practical experience would be advantageous
Experience:
Relevant Manufacturing and Leadership certification or qualification
7 years of relevant operational experience in an FMCG manufacturing environment with at least 5 years in a management position
Duties & Responsibilities
Planning:
Research and analyze best practices, local conditions, trends, and competitor activity to inform strategy.
Contribute to manufacturing strategy and execute annual objectives.
Fine-tune systems to adapt to changing work practices.
Foster integration between cross-functional processing and planning teams.
Innovate resource use for optimal output.
Establish guidelines for resource optimization and minimal resource use.
Set departmental targets aligned with plant objectives and monitor performance weekly.
Adjust production plans to meet annual targets and address production variances.
Packing and Process Management:
Drive continuous improvement in processes and procedures.
Ensure departmental capacity aligns with production plans.
Optimize resource allocation (cost, people, time) in the processing department.
Coordinate with S&OP and Milling departments for production alignment.
Manage labor resources within budget and develop talent pipelines.
Monitor and adjust manpower and equipment availability to meet production needs.
Report on departmental KPIs weekly and address non-conformances promptly.
Manage equipment performance and maintenance priorities with Engineering.
Safety, Health, Risk, Food Safety and Quality Oversight:
Establish systems and practices to comply with regulations and best practices.
Ensure compliance with safety, health, food safety, and quality standards.
Maintain FSSC 22 000 standards and related management systems.
Implement in-process quality control and sustainable environmental practices.
Maintain high housekeeping standards and develop SOPs for packing lines.
Financial Management:
Assume responsibility for the departmental budget.
Forecast, plan, and review annual budgets.
Manage input costs and address overspending.
Implement cost containment measures and business improvement initiatives.
Provide input into Capex plans and justify expenditures to senior management.
Contract Management:
Collaborate with HR and Procurement for contractor selection.
Develop SLAs for suppliers and manage contracts within the department.
Project Management:
Manage project plans and oversee implementation within the department.
Drive efficiency projects to improve execution and operational targets.
Reporting:
Ensure accurate data capture for reliable reporting and decision-making.
Utilize IT systems to analyze operational management and costs.
Adjust processing practices to optimize volume and quality.
Staff Management:
Manage capacity through RCL employees and external labor providers.
Facilitate daily planning discussions and monthly 1-on-1s.
Drive leadership development and skills enhancement.
Manage performance and conduct disciplinary actions when necessary.
Oversee training and career development plans.
Conduct operational meetings and ensure objectives are met.
Key Performance Indicators (KPIs):
Manage Processing budget versus expenditure.
Achieve planned versus actual production rate (>95%).
Reduce process waste.
Deliver on cost-saving initiatives.
Ensure SHEQ compliance.
Implement training according to plans.
Maintain staff morale and retention.
Achieve production targets (volumes, yield, line speed).
Manage labor costs and overtime effectively.
Continuous Improvement Specialist
Closing Date
2024/08/02
Reference Number
RCL240723-1
Company RCL Foods
Job Title Continuous Improvement Specialist
Functions Operations/Manufacturing
Job Type Classification Permanent
Location – Town / City Centurion
Location – Province Gauteng
Location – Country South Africa
Job Description
Join our dynamic team as a Continuous Improvement Specialist and play a pivotal role in driving our operational strategy and objectives. You will lead the implementation of short/medium-term strategic projects, analyse complex operations, workflows, and production processes to enhance efficiency, and ensure our products meet the highest quality standards. This role involves designing and overseeing systems that maximize productivity, reduce waste, and encourage cost-effectiveness through innovative cost-saving initiatives.
Minimum Requirements
B-Tech or Degree in Industrial Engineering.
5+ years of industry experience within Food or FMCG environments.
Proven experience with Lean and Continuous Improvement methodologies.
Exceptional critical and curious thinking abilities.
Strong problem-solving skills.
Excellent communication and presentation skills.
Keen attention to detail.
Deep insight into manufacturing and operations.
Proficiency in MS Office, particularly strong Excel skills.
Strong coaching and mentoring skills within Operations.
Duties & Responsibilities
Strategic Leadership:
Lead the business in driving operational strategy and objectives.
Define and implement new operational strategies, working closely with the Operational team on special projects.
Advanced Analysis and Design:
Conduct in-depth capacity planning and performance analysis.
Analyse complex operations, workflows, and production processes to identify inefficiencies.
Design control systems aimed at minimizing costs and production issues.
Project Management and Implementation:
Manage new product development plans to ensure seamless integration into plant setups.
Develop and implement comprehensive process improvements and technological upgrades.
Ensure successful and sustainable project implementation through frequent process audits and reviews.
Conduct post-implementation reviews to ensure successful delivery and identify improvements for future projects.
Training and Development:
Provide advanced training and coaching to staff on new processes, fostering a Lean culture.
Act as a catalyst for culture change towards high-performance excellence.
Continuous Improvement:
Develop tools to measure efficiencies, identify trends, and detect process variations as part of a continuous improvement system.
Advise on and initiate corrective actions to address key business metrics at risk of deviation.
Identify and motivate for new investment opportunities (CAPEX) for future growth.
Relationship Building:
Build and develop relationships with internal and external customers to address and exceed customer expectations.
Deliver coaching on new developments, processes, and ways of working.
Why Join Us? Be part of an innovative team committed to excellence and continuous improvement. With opportunities for professional growth and the ability to make a tangible impact on our operations, you’ll find a rewarding career path with us. If you are a strategic thinker with a passion for efficiency and quality, we want to hear from you.
Join us in transforming our operations and driving our business to new heights!
Electrician
Closing Date
2024/08/01
Reference Number
RCL240717-5
Company RCL Foods
Job Title Electrician
Functions Engineering
Job Type Classification Permanent
Location – Town / City Randfontein
Location – Province Gauteng
Location – Country South Africa
Job Description
RCL FOODS is seeking an Electrician to join our Groceries Division. The role will be based in Randfontein and report to the Electrical Supervisor. The successful incumbent will be responsible for the Maintenance of the electrical network and electrical equipment to ensure an efficient and reliable production flow.
Minimum Requirements
Grade 12 with Mathematics and Physical Science
N3 Electrical Technical Certificate.
Section 13 Electrical trade test.
5 Years working as qualified electrician in FMCG environment.
Solid knowledge of electronics.
Wireman Licence
PLC experience
Experience in the maintenance of flameproof equipment.
Computer literate
Able to work independently as well as a member of a team
Competencies Required
Physical strength,
Not afraid of heights.
Able to work independently as well as a member of a team.
Good organisational and planning skills as well as problem-solving.
Detail Orientated.
Decision Making
Expected to identify the nature of any problems and issues through analysis and apply judgment and initiative in order to find an appropriate/effective resolution.
Decisions to minimize the impact on factory and still guarantee good quality, relevant cost, effective productivity, without neglecting any safety standards
Problem Solving
High levels of problem solving from routine problems to complex problems which requires an innovative thinking or a creative approach and a degree of evaluation
Use their judgment to decide which course of action is the most appropriate, placing greatest emphasis on effective and timely solutions
Duties & Responsibilities
Fault finding and repair of electrical equipment
Maintenance of electrical equipment.( production lines, high speed packaging lines, dust and explosion proof equipment)
Maintenance of electrical network (HT transformers HT switches HT ring feeders and LT distribution of 14 Transformers) of 10 MVA.
Construction of new electrical equipment in plants.
Standby duty’s. and shifts
Instrumentation Technician – Randfontein
Closing Date
2024/08/01
Reference Number
RCL240717-1
Company RCL Foods
Job Title Instrumentation Technician – Randfontein
Functions Engineering
Job Type Classification Permanent
Location – Town / City Randfontein
Location – Province Gauteng
Location – Country South Africa
Job Description
RCL FOODS is seeking a qualified and a well experienced Instrumentation Technician for our Groceries Business Unit. The incumbent will be Responsible for the design, implementation and integration of PLC and Scada systems.
Minimum Requirements
Knowledge / Experience and Education
N3 Technical Certificate.
Completed Electrical trade test.
3 years PLC programming (Mitsubishi).
3 Years electronic exposure in a FMCG environment.
Knowledge of iFIX – Scada Systems.
Knowledge of packing and filling machines, metal detectors and scales.
Working knowledge on MSOffice.
Competencies Required
Able to work independently as well as a member of a team.
Must be able to demonstrate flexibility in learning new skills with regards to PLC’S and Scada systems.
Good organisational and planning skills as well as problem-solving.
Detail Orientated.
The ability to execute more than one task at the same time.
Customer Relationships
Internal
Management – weekly and monthly meetings
Colleagues and department HOD’s
Interact with employees from other departments.
External
RCL HO
Customers – with regards to equipment
Decision Making
Expected to identify the nature of any problems and issues through analysis and apply their judgement and initiative in order to find an appropriate resolution.
Decisions to minimally impact on factory quality, cost, productivity and safety standards.
Problem Solving
Levels of problem solving from routine problems to complex problems which requires an innovative thinking or a creative approach and a degree of evaluation; the Post Holder must use their judgement to decide which course of action is the most appropriate, placing greatest emphasis on effective and timely solutions.
Duties & Responsibilities
Programming, and wiring of PLC’s – Existing Factory / Equipment and new installations.
Plan, design and programming of Scada and HMI system
Commissioning of new plants – Correct starting sequence and safety circuits.
Optimization of PLC programs to increase productivity.
Fault finding/repair of factories / machinery.
Design and manufacture / repair pc boards & heater cards.
Repair of scales.
All the best with your applications.
Leave a Reply