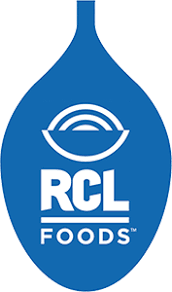
Share this post on
To apply, click on the link at the end of the posts and all the best with your applications.
NPD Process Technologist – Speciality – Centurion
Closing Date | 2024/09/13 |
Reference Number | RCL240903-9 |
Company | RCL Foods |
Job Title | NPD Process Technologist – Speciality – Centurion |
Functions | R and D |
Job Type Classification | Permanent |
Location – Town / City | Centurion |
Location – Province | Gauteng |
Location – Country | South Africa |
Job Description
At RCL Foods, we believe in growing what matters! As a leading food manufacturer, our goal is to nourish people with a portfolio of trusted brands and products. We are committed to innovation, sustainability, and the development of our employees.
We at RCL FOODS are in search for an NPD Process Technologist to join our Baking Business Unit. The role will be based in Centurion and report to the New Product Development Manager.
The NPD Process Technologist is the link between the product development kitchen and the production line. Responsible to ensure that new products make a smooth transition from trial and testing stages to full production.
The NPD Process Technologist ensures that trial factory production runs take place with the outcomes reported to all relevant staff. Identify any critical issues, make recommendations for improvements, measure yields and make sure that everything complies with quality and customer expectations
In some instances the NPD Process Technologist may also be responsible for trialling new processing equipment – either in support of a new product launch or to make improvements to current production processes.
Minimum Requirements
- Qualified Food Technologist
- Numerical and verbal aptitude, strong communicator.
- Intermediate computer skills (especially excel and word)
- A valid driving license
- Minimum 2 year’s proven experience running process trials within food manufacturing
- Processing innovation in terms of equipment/process
- NPD experience from concept to launch would be advantageous
- Exposure to either retailers or foodservice customers
- Great attention to detail and the ability to effectively manage simultaneous projects
- Excellent communication and interpersonal skills
Duties & Responsibilities
New Product Development
Responsible for the implementation of new products developed by the NPD Team in the factories that will ensure a successful product launch, ensuring that product consistency is achieved throughout the entire process
Schedule and manage production line trials and re-evaluations making sure that everything has gone to plan
Understand company production processes and flag up any potential problems to the NPD team at early development stages.
Initiate solutions to production issues / problems / capacity constraints.
Develop and co-ordinate practical schedules for product launches
Liaise with purchasing colleagues to ensure that all incoming stock for factory trial runs is in place.
Management of the critical path from the factory trial stage to ensure projects are successfully completed in line with agreed timescales and keeping key personnel aware of any updates and delays.
Technical & Quality Management
Ensure that Factory Trials take place with the outcomes reported to all relevant teams, measure yields and make sure that everything complies with customer expectations.
Facilitate customer visits during production trials.
Initiate and trial new processing equipment – either in support of a new product launch or to make improvements to current production processes.
Conduct ongoing investigations into production processes and make recommendations for improvements if necessary.
Ensure that operating procedures, quality contracts and specifications are written correctly for each new product and available to relevant staff
Technical Expertise and Insight
Identify any critical issues, and make recommendations regarding processes of equipment for improvements.
Support initial production runs and be available to troubleshoot and provide expert advice if necessary
Compile reports capturing key data, scale-up and methods, QAS, qualitative and quantitative standards, yields and process waste.
Ensuring that kitchen components and finished product samples are retained for reference and future benchmarking against 1st trial & customer launch sign-offs.
Organise and perform shelf-life and organoleptic testing of retained samples to ensure product safety and quality against agreed QAS.
Monitor any changes to the NPD recipe and processes that will result in increased product costs. Report any deviations whilst agreeing on corrective actions as appropriate.
To arrange and conduct factory trials and full scale-up 1st production runs ensuring that the technical information supporting the new product is correct and up to date.
Ensure factory manufactured products adhere to customer specifications throughout the product lifecycle by attending taste panels and customer reviews.
Diesel Mechanic – Polokwane
Closing Date | 2024/09/05 |
Reference Number | RCL240826-1 |
Company | RCL Foods |
Job Title | Diesel Mechanic – Polokwane |
Functions | Engineering |
Job Type Classification | Permanent |
Location – Town / City | Polokwane |
Location – Province | Limpopo |
Location – Country | South Africa |
Job Description
RCL believes in doing more! We are passionate about our commitment to providing more food to more people more often. The recruitment team is on the hunt for a Qualified Diesel Mechanic to be based in Polokwane.
PURPOSE OF THE POSITION
Responsible for maintaining diesel equipment operation by completing inspections and preventive maintenance requirements; correcting vehicle deficiencies; making adjustments and alignments; and keeping records.
Minimum Requirements
Matric
Valid Drivers License
Qualified Diesel Mechanic
5 years of experience in a similar role
Behavior Standards
Be brilliant at the basics
Face the brutal facts
Smash the silos
Lead with integrity, respect and energy
Be curious and challenge change
Take accountability for results and people
Knowledge
Organizational/business unit processes
The sector and its offerings
Coaching
Audit and compliance
Recent laws and regulations
Skills
Verbal and written communication
Computer literacy
Report writing
Interpersonal
Logical thinking
Analytical thinking
Decision making
Presentation and facilitation
Negotiation
Organisational awareness
Influence
Attributes
Persuasive
Initiative and assertive
Tolerant of stress and pressure
Creative
Proactive
Attention to detail
Deadline driven
People orientated
Able to interact at all levels of the organisation
Results/Goal oriented
Able to encourage and motivate people
Duties & Responsibilities
- Determines vehicle condition by conducting inspections and diagnostic tests; identifying worn and damaged parts.
- Keeps equipment available for use by completing preventive maintenance schedules; installing component and part upgrades; controlling corrosion; completing winterization procedures.
- Corrects vehicle deficiencies by removing, repairing, adjusting, overhauling, assembling, disassembling, and replacing major assemblies, sub-assemblies, components, parts, or systems, such as, power and drive trains, electrical, air conditioning, fuel, emission, brake, steering, hydraulics; completes machine shop operations; making adjustments and alignments including bearing loads, gear tooth contact, valve mechanisms, governors, oil systems, control linkages, clutches, and traction units.
- Verifies vehicle performance by conducting test drives; adjusting controls and systems.
- Complies with federal and state vehicle requirements by testing engine, safety, and combustion control standards.
- Maintains vehicle appearance by cleaning, washing, and painting.
- Maintains vehicle records by annotating services and repairs.
- Keeps shop equipment operating by following operating instructions; troubleshooting breakdowns; maintaining supplies; performing preventive maintenance; calling for repairs.
- Contains costs by using warranty; evaluating service and parts options.
- Keeps supplies ready by inventorying stock; placing orders; verifying receipt.
- Updates job knowledge by participating in educational opportunities; reading technical and regulation publications.
- Enhances maintenance department and organization reputation by accepting ownership for accomplishing new and different requests; exploring opportunities to add value to job accomplishments.
All the best with your applications.
Leave a Reply