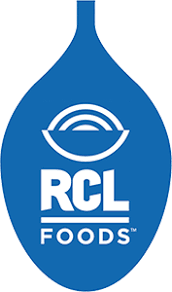
Share this post on
To apply, click on the link at the end of the posts and all the best with your applications.
Depot Controller
Closing Date | 2024/09/29 |
Reference Number | RCL240919-4 |
Company | RCL Foods |
Job Title | Depot Controller |
Functions | Supply Chain |
Job Type Classification | Permanent |
Location – Town / City | Welkom |
Location – Province | Free State |
Location – Country | South Africa |
Job Description
Our Talent Teamis looking for a Depot Controller to join their Baking Business Unit. This position is located in Welkom and will report to the General Manager.
The successful incumbent will be responsible for managing and maintaining the fleet and the transport team in the depot, thereby ensuring that productivity and performance are maximized. To control the inbound and outbound processes and stock handling in order to maintain efficiencies within the depot warehouse and Maintain a sound reconciliation process of all stock and drivers reconciliation
Minimum Requirements
A 3-year national diploma in logistics, fleet and/or warehouse management.
Valid Code EB drivers’ license.
Computer literacy (MS Office).
A minimum of 3 years management experience in a similar environment.
Minimum of 3-5 years’ experience in an FMCG environment.
Previous experience managing warehousing, distribution, and stock control.
Duties & Responsibilities
Inbound Control:
Control the inbound process by receiving products in good condition.
Manage the capturing of stock on the SAP system to ensure that goods are controlled and easily identified.
Ensure the product is allocated to the right bin in order to facilitate ease of access and convenience as and when required.
Activate internal material movement, incorporating order placement; product picking; and movement to truck for dispatch.
Monitor product shelf life in order to ensure the product has not expired, using the FIFO (first in, first out) system.
Outbound Control:
Control the functions of outbound, ensuring products are dispatched out to customer.
Ensure that all orders leave the warehouse correctly packed and damage free.
Ensure all invoicing has been completed accurately and correct where necessary.
Manage and facilitate the process of loading goods onto trucks and ensure all products are sealed for transport to customers.
Customer Liaison:
Deal with issues around damaged stock or stock shortages.
Check that details on invoices coincide with those on the orders.
Notify customers should any transport incident have a likely impact on delivery.
Schedule customer deliveries according to the time window process.
Verify orders and liaise with customers on point of receiving, making use of the SAP System.
Stock Control:
Ensure stock is in the right location through the management of daily cyclic counts.
Ensure staff are properly rotating stock (where it does not go to the pick face but to the back-up location).
Monitor production and expiry dates on all inbound and outbound products.
Track inbound/outbound damage trends, establish root causes and take the appropriate corrective action.
Ensure cyclic counts are conducted prior to stock takes.
Ensure frozen stock is kept in the appropriate frozen and/or chilled state.
Prepare for and initiate monthly stock takes, ensuring that the entire process is completed within specified time frames.
Warehouse Maintenance Management:
Manage and monitor the condition of the warehouse ensuring that the warehouse is kept clean. Damaged goods are dealt with according to SoP. Lighting is adequate and doors open and close easily. Areas in need of attention are reported to the Maintenance Manager. All bin allocations are clear from any damaged pallets. All forklifts are in good working conditions.
Fleet Control:
Manage the daily schedule.
Check that a job card has been allocated to work and that the driver has managed to complete the form correctly.
Ensure that drivers complete the checklist every morning and afternoon to establish if there are any defaults.
Request complaints and difficulties for the day and take the appropriate action.
Monitor transport performance against benchmarks by obtaining vehicle exception reports from the tracking department as a means of monitoring drivers’ conduct and vehicle performance.
Compliance Control:
Handle proxy responsibilities.
Ensure that all drivers have valid driver’s licences and PDP’s.
Ensure all staff members comply with health and safety requirements.
Investigate and report on all injuries on duty (IOD’s).
Implement safe working procedures.
Verify temperature for the entire warehouse by analysing the temperature worksheet.
Ensure frozen stock is maintained at above minus 18 and chilled not below minus 1.
Ensure staff understand and comply with the standards set by ISO 22 000 and HACCP.
Certify that a new load always enters a clean and well maintained vehicle highlighting the significance of quality.
Security Control:
Investigate hijacking incidents to establish whether or not they are genuine cases.
Ensure that all stock leaves the warehouse with proper documentation.
Ensure cameras are focused on risk areas such as entry and exit points and on staff activity/inactivity to ensure staff are appropriately utilised and productive.
Issue stock counts on key lines such as “ready to eat” products (e.g. polony) on a daily basis and analyse results.
Ensure that security staff check staff leaving for tea and lunch breaks.
Ensure all trucks leaving the warehouse are sealed and recorded in a sealed register.
Check the seals on warehouse doors on a daily basis.
Team Supervision:
Train staff on the Standard Operating Procedures that serve to guide their approach to work.
Implement the Standard Operating Procedures through consistent application and communication.
Ensure that staff understand the procedures and sign off the relevant documents.
Conduct monthly meetings with staff in order to ascertain problems encountered and resolve associated issues.
Manage staff performance in order to establish opportunities for development and harness strengths.
Supply Planning Manager
Closing Date | 2024/09/27 |
Reference Number | RCL240916-2 |
Company | RCL Foods |
Job Title | Supply Planning Manager |
Functions | Supply Chain |
Job Type Classification | Permanent |
Location – Town / City | Pretoria West |
Location – Province | Gauteng |
Location – Country | South Africa |
Job Description
As a leading player in the Food Manufacturing industry, we pride ourselves on delivering high-quality products and making a positive impact. As we continue to grow, we are seeking a talented and motivated individual to join our team as a Supply Planning Manager to optimize our supply chain, ensure exceptional customer service, maximize profitability, and drive innovation
The role reports to the Supply Chain Executive within the Beverages Business Unit and is based in Pretoria West.
The primary objective of this position is to:
manage the creation and delivery of both the short term and longer-term business supply plans, up to a 24-month horizon, in order to optimise customer service, maximize profit in terms of product mix, minimise cost (processing, distribution and working capital) and facilitate the overall supply chain delivery of innovation.
manage the ordering process of packaging and ingredients, as well as the physical management of the packaging and ingredients stores, and associated stock levels (including stock accuracy and obsolescence). Responsibility includes determining when Finished Goods or raw materials need to be procured either locally or imported to supplement inhouse production. This may also mean working with the commodities procurement team in order to secure key materials,
manage the loading and despatch of Finished Goods to meet customer delivery requirements (time slots, delivery equipment and snake loading) and ensure all commercial requirements are reconciled with the finance team.
Minimum Requirements
Qualification
Relevant 3 year degree or Supply Chain Diploma
Skills and Experience
7 years of experience in the supply chain, with a minimum of 3 years in a management position
Strong knowledge of supply chain principles, demand planning, and production processes
Proficiency in SAP or other ERP systems
Excellent analytical, problem-solving, and decision-making skills
Strong interpersonal and communication skills
Duties & Responsibilities
Strategic Planning
Develop a forward supply plan for 12-24 months based on demand forecasts.
Identify capacity constraints and provide input for capital expenditure discussions.
Contribute to the 5-year strategic planning process when needed.
Functional Strategy into Action Operationalisation
Collaborate with Senior Managers to create a supply chain strategy for 1-2 years.
Manage relationships with cross-functional teams to ensure integrated supply chain delivery.
Contribute to and implement the annual “Strategy into Action” plan through team targets.
Supply Planning of Finished Goods and Key Input Materials
Balance the national supply plan against the demand plan for the next 18-24 months.
Ensure customer demand is met while maximizing profitability and minimizing costs.
Manage Rough Cut Capacity Plans (RCCP) to meet customer service, stock, and cost targets.
Provide forward space and stock movement plans to the Supply Chain Executive.
Short Term Supply Planning (Production Planning and MRP Call-off)
Develop detailed production plans considering various constraints.
Ensure materials requirements plans support production without impacting it.
Prioritize products to maintain stock covers and align with profit goals.
Stock Management (Finished Goods, Raw Materials, Packaging, and Ingredients)
Manage national stock covers to meet customer service, profitability, and cost targets.
Use stock modeling tools to drive improvements in working capital and customer service.
Proactively manage stock covers, considering capacity constraints and product changes.
Material Requirements Planning (Packaging & Ingredients)
Ensure the national material requirements plan meets forward packaging and ingredients needs.
Work with procurement to reduce stock holding and complexity.
Oversee packaging and ingredients stores to maintain appropriate stock levels and protect stock.
Distribution Management
Manage the dispatch environment to meet customer service targets efficiently.
Ensure customer delivery requirements are met, including loading specifications.
Manage and maintain the fleet and transport team where applicable.
Sales and Operations Planning
Contribute to demand planning and continuous improvement within the S&OP process.
Collaborate with Supply Chain and Commercial teams to balance supply and demand, identify supply gaps, and suggest solutions or product substitutions.
Lead national Supply Planning input into the S&OP process.
Ensure warehousing and transport plans meet demand plans.
Drive continuous improvement using agreed KPIs.
Innovation/Discontinuation
Manage innovation planning, production planning, and the introduction or discontinuation of products.
Control costs associated with discontinuation and keep business forums updated.
Supply Chain Reporting
Measure and report national KPIs monthly.
Use KPIs to drive action plans and improve customer service across regional planning teams and other functions.
Project Management / Participation
Participate in projects aimed at improving supply chain processes, reducing costs, and enhancing technology.
Administration
Oversee record-keeping, compile spreadsheets, and process inter-company charge outs.Staff Management
Monitor and provide feedback on staff performance.
Ensure service levels are met and protocols followed.
Support staff development and manage succession plans.
Promote staff training and development opportunities.
All the best with your applications
Leave a Reply