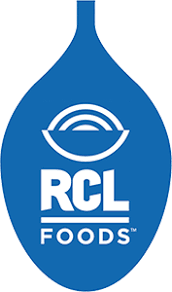
Share this post on
To apply, click on the link at the end of the posts and all the best with your applications.
Maintenance Planner – Krugersdorp
Closing Date | 2024/09/15 |
Reference Number | RCL240905-4 |
Company | RCL Foods |
Job Title | Maintenance Planner |
Functions | Engineering |
Job Type Classification | Permanent |
Location – Town / City | Krugersdorp |
Location – Province | Gauteng |
Location – Country | South Africa |
Job Description
RCL Foods is seeking Maintenance Planners to join our Baking Pies Business Unit. The role will be based in Krugersdorp.
Purpose of the Role: To provide logistic support to the maintenance team by ensuring plant activities are planned well ahead of time in order to enhance equipment availability. This will be done by administrating the maintenance management system, monitoring and generating reports on maintenance performance for management decision-making
Minimum Requirements
Grade 12 or N3 or NCV Technical qualifications
Certificate in maintenance planning and scheduling
Experience and Training
3 years’ maintenance experience in FMCG
Formal maintenance training
Knowledge and Skill
A working knowledge of Computerised Maintenance Management Systems(CMMS).
Knowledge of Store Inventory Management System
An understanding of engineering machines components such as shafts, bearings, v-belts, drives, contactors, conveyors, etc
Knowledge of food safety standards is advantageous
Supervision of personnel added advantage
Problem-Solving
Ability to think logically and problem-solving
Ability to interpret the data and analyze
Ability to analyze the trends in performance parameters
Customer Relationships
Internal
Liaise with production management and machine operators and staff.
Liaise with Ecowise cleaning team and management
External
Liaise with suppliers and contractors
Decision Making
Decide on which parts needs replacement and any additional work required in daily basis
Decide on additional activity that is required to improve performance of the machines
Report any defects pickup during machine stripping to ensure is correct either immediately or during the weekend activities
Competencies
Must be proficient with word, excel and PowerPoint and Computerized Maintenance System
Demonstrate high degree of planning and organizational skills
Strong communication skills
Read, analyze, understand electrical, electronic and engineering drawings and tolerances
Work in the framework of a team
Attention to detail and deadline driven
Adhere to principles and values
Apply good governance principles
Build interpersonal tolerance and teamwork practices
Must conform to contractual obligations
Be prompt and courteous
Training on root cause analysis
Logical reason
Individual must be able to work productively within a team
Communication
Ability to communicate well at all levels
Ability to read and write
Duties & Responsibilities
Establish, maintain and improve the maintenance planning and scheduling business flow process.
Prepare reports, analyse data and make recommendations for improving plant operations and solving maintenance related problems.
Ensure key performance indicators are captured and reported for equipment reliability, departmental performance, planning and scheduled business flow process.
Schedule maintenance work into production plan.
Develop cost and time estimate of planned maintenance work.
Review applicable maintenance procedures that promote defect-free maintenance work quality.
Identifies, analyses, and reviews equipment maintenance problems with maintenance engineering team.
Responsible for up-keep and accuracy of equipment maintenance history and jobs records database.
Continually improving planning, scheduling, data management and job reporting systems to increase planning effectiveness and efficiency.
Collaborate with maintenance Senior Artisans to schedule manpower and resource for planned maintenance work.
Assists in educating operations personnel in maintenance management.
Perform any other related job that may be assigned from time to time.
Maintenance Storeman
Closing Date | 2024/09/14 |
Reference Number | RCL240904-2 |
Company | RCL Foods |
Job Title | Maintenance Storeman |
Functions | Engineering |
Job Type Classification | Permanent |
Location – Town / City | Rustenburg |
Location – Province | North-West |
Location – Country | South Africa |
Job Description
KEY RESPONSIBILITIES
- Daily stock takes.
- Interaction with Suppliers, Quote requests.
- Ordering of Parts and Consumables.
- Manage Stock Levels.
- Receiving and Issuing of Parts.
- Opening and managing of Jobcards.
- Matching of Daily Invoice.
- Monthly Stocktakes.
- Issuing of Tools and Daily recon of Special Tools.
- Parts store control.
- Assisting Buyer with quotes and ordering of parts.
- Do Daily housekeeping.
- Problem solving.
- Do regular filling during the month.
Minimum Requirements
QUALIFICATION AND EXPERIENCE
- Grade 12.
- A formal qualification would be an added advantage
- Drivers Licence and PDP will be added advantage
- Minimum 2 years’ experience in an FMCG environment
KNOWLEDGE AND SKILLS REQUIREMENTS
- Organised
- Ability to work under pressure.
- Must be a self-starter and have the ability to use own initiative
- Must be able to communicate with people on all levels.
PRIMARY JOB OUTPUTS
- The successful incumbent will be responsible for Internal procurement controls. Internal departments stock control as directed by the Maintenance Manager.
- Successful candidates will be working shifts, weekends (including Sunday), overtime and public holidays as and when required
Duties & Responsibilities
KEY RESPONSIBILITIES
Daily stock takes.
Interaction with Suppliers, Quote requests.
Ordering of Parts and Consumables.
Manage Stock Levels.
Receiving and Issuing of Parts.
Opening and managing of Jobcards.
Matching of Daily Invoice.
Monthly Stocktakes.
Issuing of Tools and Daily recon of Special Tools.
Parts store control.
Assisting Buyer with quotes and ordering of parts.
Do Daily housekeeping.
Problem solving.
Do regular filling during the month.
Maintenance Assistant
Closing Date | 2024/09/14 |
Reference Number | RCL240904-1 |
Company | RCL Foods |
Job Title | Maintenance Assistant |
Functions | Operations/Manufacturing |
Job Type Classification | Permanent |
Location – Town / City | Rustenburg |
Location – Province | North-West |
Location – Country | South Africa |
Job Description
KEY RESPONSIBILITIES
Perform daily maintenance work
Work with engineering department to complete projects
Complete daily tasks at a reasonable pace and quality
Do daily inspection and give feedback
React timeously to breakdowns.
Assist Artisan overhauling and assembling equipment.
Adhere to safety rules and regulations.
Perform ad hoc tasks as required by Management.
Be able to fit into different team and preparedness to be moved around as needed.
Duties & Responsibilities
KEY RESPONSIBILITIES
Perform daily maintenance work
Work with engineering department to complete projects
Complete daily tasks at a reasonable pace and quality
Do daily inspection and give feedback
React timeously to breakdowns.
Assist Artisan overhauling and assembling equipment.
Adhere to safety rules and regulations.
Perform ad hoc tasks as required by Management.
Be able to fit into different team and preparedness to be moved around as needed.
Maintenance Administrator
Closing Date | 2024/09/13 |
Reference Number | RCL240903-5 |
Company | RCL Foods |
Job Title | Maintenance Administrator |
Functions | Engineering |
Job Type Classification | Permanent |
Location – Town / City | Pretoria West |
Location – Province | Gauteng |
Location – Country | South Africa |
Job Description
At RCL FOODS we see and do things differently, we think bigger, work smarter and as a team collectively work towards achieveing our ambition, to Grow What Matters!
RCL FOODS is currently requiring for a Maintenance Administrator to join our Milling Division that is based in Pretoria West. The successful individual must have passion for people, analytics, building collaborative relationships and driving brilliance. The role will report into the Senior Maintenence Planner.
As the maintenance administrator you will assist the clients (production and engineering) to continuously improve their overall equipment effectiveness, by implementing and administering effective asset management systems and procedures, particularly in the areas of information management, work planning & control, performance measurement, maintenance tactics and spares & materials through the effective delegation and management of available resources.
Minimum Requirements:
A recognised trade test
N3 technical qualification (minumum)
2+ Year of Pragma Onkey experience.
BestTime or similar personnel time account experience.
Minimum of 2 years experience as Maintenance Planner in the Fast Moving Consumer Goods (FMCG) industry.
2 to 3 Years’ experience in asset and asset care management Auditing experience advantageous.
2-3 years supervision experience is advantageous.
Advanced skills in Microsoft Office- Namely MS Outlook, Excel, Powerpoint, Projects and Word.
Key Responsibilities
A working knowledge Computerised Maintenance Management Systems(CMMS). Specific preference is given to Pragma Onkey (Onkey 5/ Onkey 5 Plus).
Knowledge of Store Inventory Management Systems and techniques.
An understanding of engineering machines components such as shafts, beraings , v-belts, drives, contactors, conveyors, motors, circuit breakers, etc.
Knowledge of food safety standards is advantageous
Adhering to all safe working procedures available in the safety manuals.
Good communication skills towards all levels within the company
Be a methodical and systematic worker, comfortable in an office environment with a fair amount of paperwork.
Practical in ensuring the success of maintenance execution by actively monitoring progress on the shopfloor and conducting job observations.
Must have a pro-active problem-solving approach in the anticipation of problem areas and taking corrective actions to eliminate deviations.
Be goal orientated, stable, show integrity and be able to make decisions under pressure
Effective leadership skills and experience in handling IR related problems
Minimum Requirements
A recognised trade test
N3 technical qualification (minumum)
2+ Year of Pragma Onkey experience.
BestTime or similar personnel time account experience.
Minimum of 2 years experience as Maintenance Planner in the Fast Moving Consumer Goods (FMCG) industry.
2 to 3 Years’ experience in asset and asset care management Auditing experience advantageous.
2-3 years supervision experience is advantageous.
Advanced skills in Microsoft Office- Namely MS Outlook, Excel, Powerpoint, Projects and Word.
Duties & Responsibilities
A working knowledge Computerised Maintenance Management Systems(CMMS). Specific preference is given to Pragma Onkey (Onkey 5/ Onkey 5 Plus).
Knowledge of Store Inventory Management Systems and techniques.
An understanding of engineering machines components such as shafts, beraings , v-belts, drives, contactors, conveyors, motors, circuit breakers, etc.
Knowledge of food safety standards is advantageous
Adhering to all safe working procedures available in the safety manuals.
Good communication skills towards all levels within the company
Be a methodical and systematic worker, comfortable in an office environment with a fair amount of paperwork.
Practical in ensuring the success of maintenance execution by actively monitoring progress on the shopfloor and conducting job observations.
Must have a pro-active problem-solving approach in the anticipation of problem areas and taking corrective actions to eliminate deviations.
Be goal orientated, stable, show integrity and be able to make decisions under pressure
Effective leadership skills and experience in handling IR related problems
Production Manager
Closing Date | 2024/09/08 |
Reference Number | RCL240829-1 |
Company | RCL Foods |
Job Title | Production Manager |
Functions | Operations/Manufacturing |
Job Type Classification | Permanent |
Location – Town / City | Krugersdorp |
Location – Province | Gauteng |
Location – Country | South Africa |
Job Description
Join our dynamic team at RCL Foods as a Production Manager in the Pies Division, where you will be responsible for managing our manufacturing processes, equipment, and facilities. Your focus will be on maximizing efficiency, ensuring compliance with industry standards, and driving innovation in our production practices.
Minimum Requirements
Diploma or Degree in Production Management or related field.
7 years of relevant operational experience in an FMCG manufacturing environment, with at least 5 years in a management role.
Duties & Responsibilities
Production Planning & Management:
- Develop and execute production strategies to achieve production targets efficiently.
- Monitor and adjust production plans to ensure alignment with business goals.
- Collaborate with cross-functional teams to optimize resource utilization.
- Lead continuous improvement initiatives to enhance production effectiveness.
Safety, Health, Quality & Environmental (SHEQ) Compliance:
- Ensure compliance with all relevant legislation, standards, and best practices.
- Drive adherence to ISO standards and promote a culture of safety and quality.
- Oversee in-process quality control to meet customer and regulatory requirements.
Financial & Resource Management:
- Manage the production budget, monitor spending, and implement cost-saving initiatives.
- Oversee resource allocation to ensure optimal productivity and efficiency.
- Lead the development and implementation of Capex projects to enhance production capacity.
Team Leadership:
- Lead, mentor, and develop a high-performing production team.
- Foster a positive work environment that encourages innovation and accountability.
- Manage employee relations, ensuring alignment with company policies and legislation.
Project Management:
- Oversee the execution of production-related projects, ensuring timely and successful implementation.
- Collaborate with the procurement team to manage contracts and supplier relationships effectively.
Reporting & Analysis:
- Ensure accurate data collection and reporting to support decision-making.
- Analyze production metrics to identify trends and drive improvements in operations.
Behavioral Standards:
- Lead with integrity, respect, and energy.
- Embrace change and drive continuous improvement.
- Take accountability for results and people.
Skills & Knowledge:
- Strong understanding of production principles, equipment maintenance, and operations.
- Expertise in cost management, team leadership, and problem-solving.
- Excellent communication, planning, and organizational skills.
- Knowledge of SHEQ systems and labour relations legislation.
Attributes:
- Results-oriented and deadline-driven.
- Resilient and adaptable to changing situations.
- Innovative with a strong analytical mindset.
Why Join Us?
At RCL Foods, we value innovation, integrity, and continuous improvement. We offer a supportive environment where you can make a significant impact, grow your career, and be part of a team dedicated to producing high-quality products.
Application:
If you are ready to take on this exciting challenge and contribute to our success, apply now!
Diesel Mechanic – Polokwane
Closing Date | 2024/09/05 |
Reference Number | RCL240826-1 |
Company | RCL Foods |
Job Title | Diesel Mechanic – Polokwane |
Functions | Engineering |
Job Type Classification | Permanent |
Location – Town / City | Polokwane |
Location – Province | Limpopo |
Location – Country | South Africa |
Job Description
RCL believes in doing more! We are passionate about our commitment to providing more food to more people more often. The recruitment team is on the hunt for a Qualified Diesel Mechanic to be based in Polokwane.
PURPOSE OF THE POSITION
Responsible for maintaining diesel equipment operation by completing inspections and preventive maintenance requirements; correcting vehicle deficiencies; making adjustments and alignments; and keeping records.
Minimum Requirements
- Matric
- Valid Drivers License
- Qualified Diesel Mechanic
- 5 years of experience in a similar role
Behavior Standards
- Be brilliant at the basics
- Face the brutal facts
- Smash the silos
- Lead with integrity, respect and energy
- Be curious and challenge change
- Take accountability for results and people
- Knowledge
- Organizational/business unit processes
- The sector and its offerings
- Coaching
- Audit and compliance
- Recent laws and regulations
Skills
- Verbal and written communication
- Computer literacy
- Report writing
- Interpersonal
- Logical thinking
- Analytical thinking
- Decision making
- Presentation and facilitation
- Negotiation
- Organisational awareness
- Influence
Attributes
- Persuasive
- Initiative and assertive
- Tolerant of stress and pressure
- Creative
- Proactive
- Attention to detail
- Deadline driven
- People orientated
- Able to interact at all levels of the organisation
- Results/Goal oriented
- Able to encourage and motivate people
Duties & Responsibilities
- Determines vehicle condition by conducting inspections and diagnostic tests; identifying worn and damaged parts.
- Keeps equipment available for use by completing preventive maintenance schedules; installing component and part upgrades; controlling corrosion; completing winterization procedures.
- Corrects vehicle deficiencies by removing, repairing, adjusting, overhauling, assembling, disassembling, and replacing major assemblies, sub-assemblies, components, parts, or systems, such as, power and drive trains, electrical, air conditioning, fuel, emission, brake, steering, hydraulics; completes machine shop operations; making adjustments and alignments including bearing loads, gear tooth contact, valve mechanisms, governors, oil systems, control linkages, clutches, and traction units.
- Verifies vehicle performance by conducting test drives; adjusting controls and systems.
- Complies with federal and state vehicle requirements by testing engine, safety, and combustion control standards.
- Maintains vehicle appearance by cleaning, washing, and painting.
- Maintains vehicle records by annotating services and repairs.
- Keeps shop equipment operating by following operating instructions; troubleshooting breakdowns; maintaining supplies; performing preventive maintenance; calling for repairs.
- Contains costs by using warranty; evaluating service and parts options.
- Keeps supplies ready by inventorying stock; placing orders; verifying receipt.
- Updates job knowledge by participating in educational opportunities; reading technical and regulation publications.
- Enhances maintenance department and organization reputation by accepting ownership for accomplishing new and different requests; exploring opportunities to add value to job accomplishments.
All the best with your applications.
Leave a Reply